Driving change: remote collaboration in the automotive sector
Electric vehicles, connected cars and XR on the factory floor – it's an exciting time for the automotive industry. Find out how XR is making a difference today.
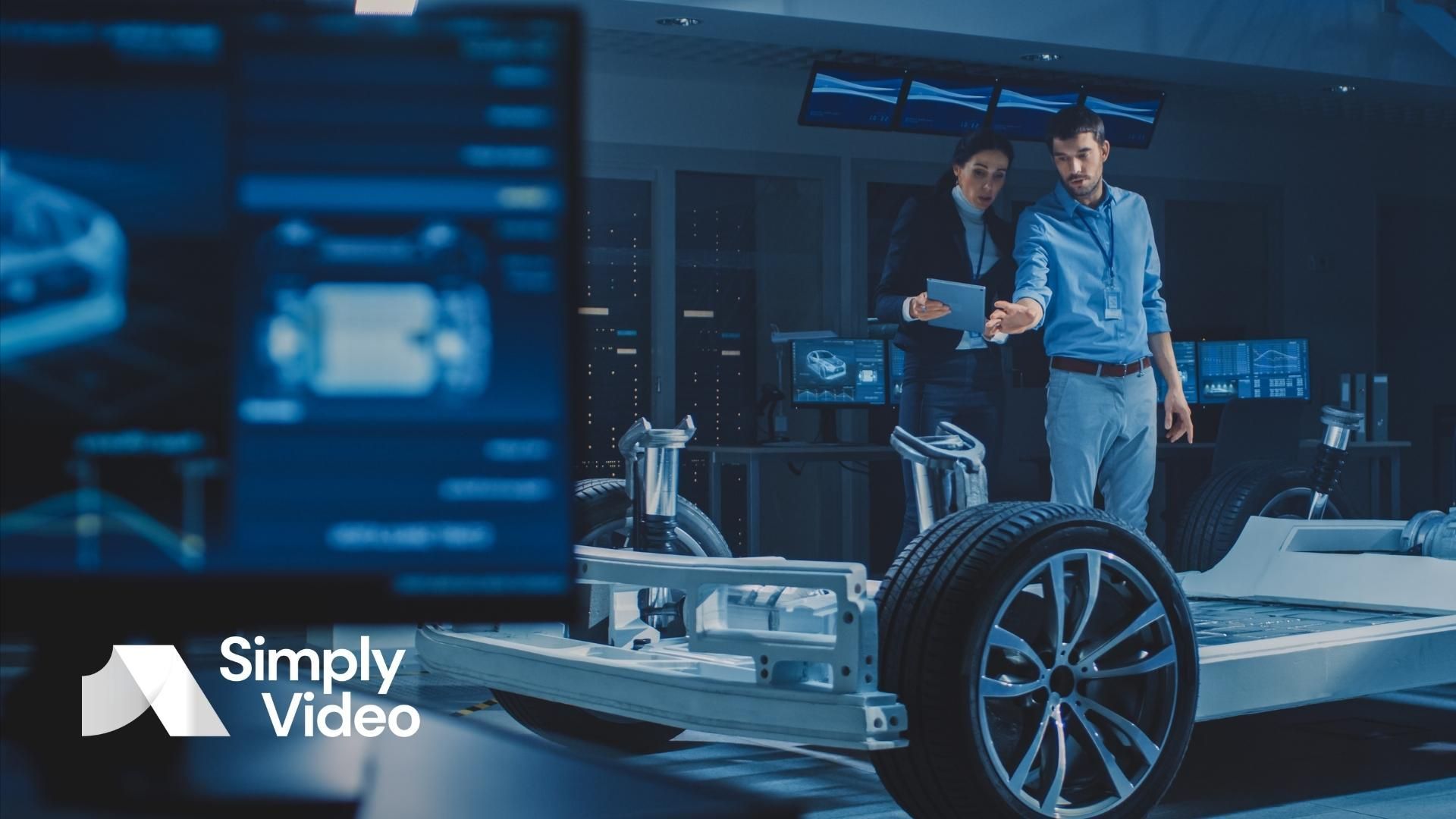
When future historians look back on the 2020s, they may well zero in on the rapid advances and changes being made in the automotive industry.
These are changes that are tied up with the climate crisis. With governments aiming for net zero, it's incumbent on the car industry to meet demand with electric vehicles.
Then there's the new phenomenon of connected cars. These are vehicles that can be operated via a smart device – an example of the ever-growing Internet of Things.
These are changes that consumers see and enjoy. But behind the scenes, something equally dramatic is going on. The automotive industry is going virtual.
More and more car companies are embracing extended reality (XR) – the family of technologies that includes virtual reality (VR) and augmented reality (AR) – both at the design stage and on the factory floor.
In the process, they're streamlining operations, cutting carbon emissions and catering to the new hybrid work model.
Here at SimplyVideo, we provide a remote collaboration software platform that's built for use with any device on any browser – and is tailor-made for bandwidth-limited environments. In this article, we take a look at how XR and remote collaboration are driving change.
VR at the design stage
Where does a car design begin? It could be a biro sketch on the back of a napkin or Chinese takeaway menu. It could be a pencil sketch in a notebook. At some point, this initial idea gets transferred to a tablet, iPad or laptop.
This preliminary sketch then gets turned into a sophisticated 3D model. Yesterday's clay mock-ups have been replaced by today's 3D-printed prototypes – and, increasingly, 3D asset visualisation.
These are full-scale models of designs – vivid, accurate, 360° visualisations that you can walk around as though they were there in the room with you.
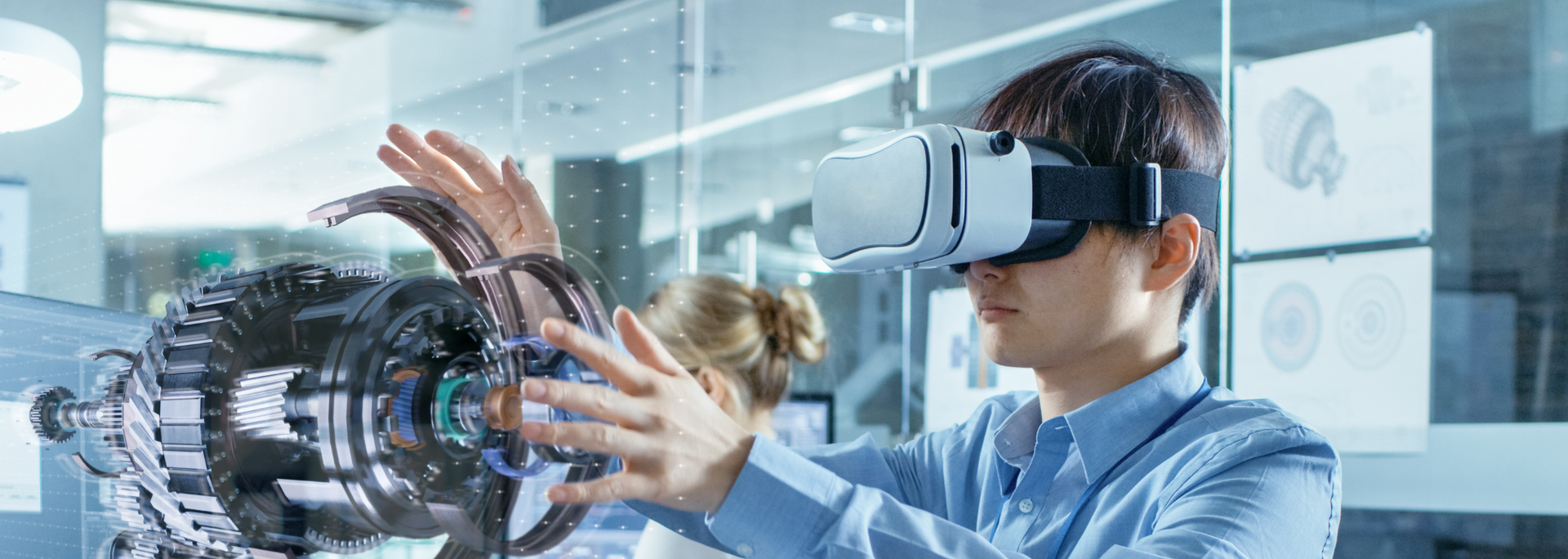
This has two key benefits. First, it enables a global team to collaborate on a project in real time. So long as all members of the team are fitted out with XR headsets, they can handle, inspect and rotate objects as though they were real.
Needless back-and-forth is eliminated ("Just chasing up my last email. Have you had a chance to...?
ad infinitum.) Collaboration becomes clear, fast and efficient.
Secondly, it widens the recruitment pool for employers. Any car manufacturer wants the cream of the crop on its team. Previously, geography was a barrier – but today, XR allows for seamless collaboration across continents.
Oh, and it saves you money. 3D printing doesn't come cheap, after all.
3D asset visualisation is a key feature of SimplyVideo when used on AR devices like Magic Leap 2. It helps you to shorten the design cycle and unlock cost savings.
Remote assistance
The design process can be assisted with VR. This is the most immersive variety of XR – the type of experience that makes users feel as though they've been plunged into a virtual environment.
AR is less immersive – but no less powerful in an industrial setting.
Where VR gives you full immersion, AR adds an extra visual layer to your actual surroundings. It's essentially an industrial version of those filters you get on Snapchat and Instagram – but instead of giving your head a halo, you're superimposing graphics and text onto the manufacturing environment.
Say an employee is looking at a car and needs a bit of help. With an AR headset or pair of smart glasses, they can link up with the expert they need in an instant – all it takes is a single click or a simple voice command.
As well as facilitating hands-free, AR-enhanced voice and video calls, XR tech can also automate guidance for staff.
This could take the form of step-by-step guidance or safety regulations, floating unobtrusively in the user's line of vision.
These floating graphic displays mean that users can stay focused on the task at hand – a welcome reduction in cognitive load.
Many of the devices on the market today are comfortable, rugged and built for industrial use – meaning that staff can wear them for long periods without discomfort.
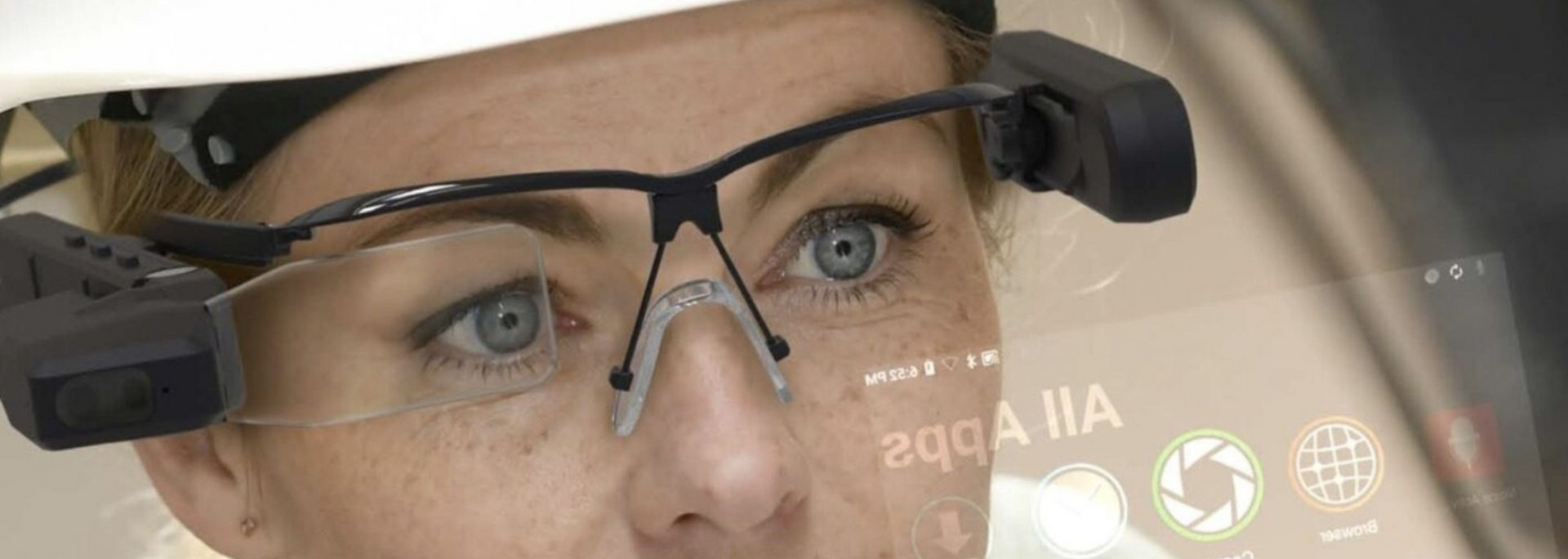
As with the design process, this empowers staff to keep up flexible or hybrid working patterns – and enables management to slash their carbon emissions.
SimplyVideo provides a version of this in the form of "in-call annotation". This is a feature where a frontline staff member can capture images or video with their headset and send them to a remote expert. The expert can then annotate the image or video to speed up troubleshooting.
You wouldn't believe how much more efficient this is than spelling out what the problem is to someone who's not there and can't see the problem.
XR and after-sales
In the automotive industry, XR doesn't end on the factory floor. It can also be used to improve after-sales services.
Even your best technician will sometimes hit a wall and need help from someone who's not in today. Time was that you would fix this by arranging for an expert to come onsite and take a look.
The problem with this traditional model is that it keeps your customer waiting. While you're fixing a date with an offsite engineer, they're twiddling their thumbs – and possibly thinking of looking for help elsewhere.
In conjunction with XR headsets, remote collaboration tools like SimplyVideo bypass this problem by instantly connecting technicians and experts with high-quality video or audio.
As with remote collaboration on the factory floor, this speeds up the problem-solving process. The company gets to clear their repair backlog more quickly – and the customer gets their vehicle back sooner.
Conclusion
From design to assembly to after-sales, VR and AR technologies can streamline operations, cut costs and enhance remote collaboration – and here at SimplyVideo, we're proud to be part of this sea change.
At SimplyVideo, we provide a low-bandwidth video
collaboration platform that's ideal for connecting with customers and clients.
Sign up today for a free 30-day trial.
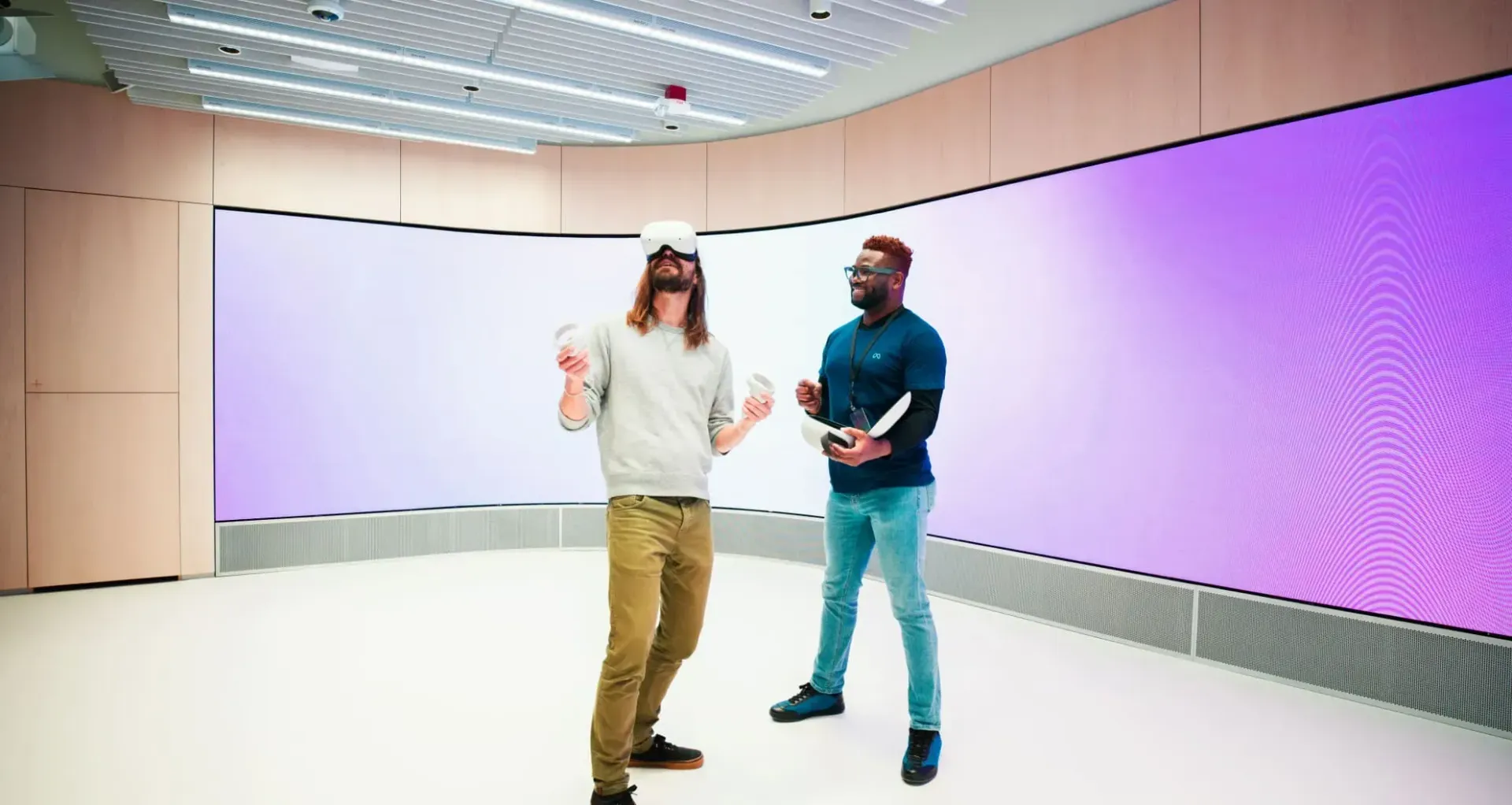