How extended reality can streamline your design process
Did you know that extended reality is transforming the way that designers work? Find out more in our bitesize guide to XR and product design.
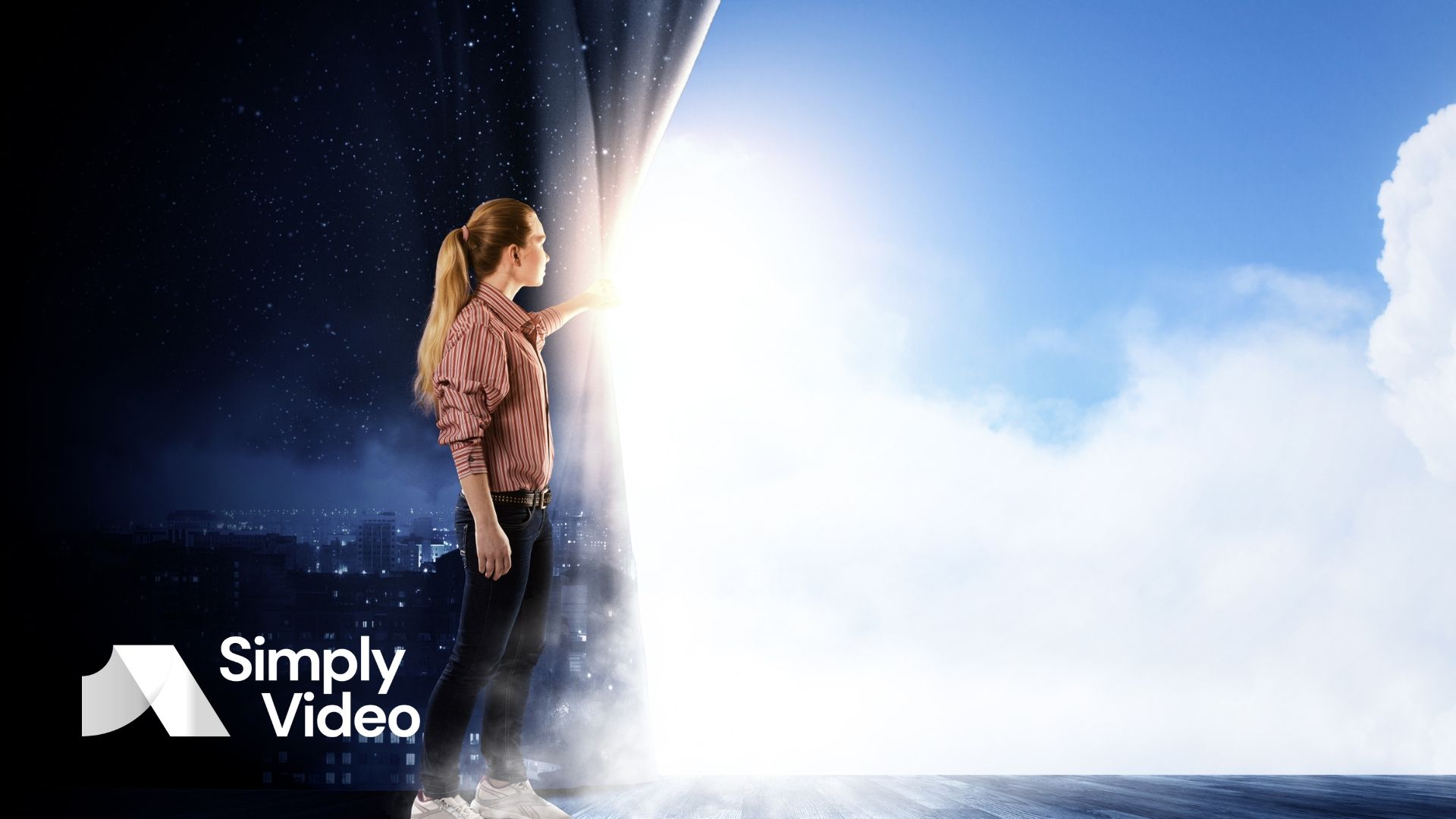
Are you frustrated with the speed of your design process? Do you wish there could be a quicker route from concept to design to reality?
How familiar does this scenario sound? Your design project involves a multiplicity of designers and stakeholders with competing calendars. Getting everyone on the same Zoom call is an uphill struggle – let alone getting them around the same table.
Or how about this: you've explored 3D CAD and 3D printing but still find yourself struggling to communicate to focus groups and stakeholders just
why they should believe in your vision.
If this sounds like you, it may be time to slip on a headset and enter the world of XR.
XR – or extended reality – has the power to transform a range of sectors. It's being used up on the oil rig, down on the factory floor and out in the field. And the world of design is no exception, whether you're creating consumer goods or skyscrapers.
The headline is that XR allows you to visualise and interact with blueprints with a whole new level of tactility and detail. Designers, users and stakeholders can all take apart the product and see how it works as though it were real.
It's our belief that XR can bring ideas to life with unparalleled speed and flexibility. It can speed up approvals. And it can cut both travel costs and carbon emissions. Win, win, win.
But before we delve into the details, let's define some terms. So far we've been talking about XR – but how is that different from its similarly named cousins, VR, AR and MR?
A very brief guide to XR
Extended reality is an umbrella term. To take an analogy from science, XR is the domestic dog, while VR, MR and AR are different breeds. As well as encompassing these different types of immersive technology, it can incorporate artificial intelligence (AI) and the internet of things (IoT).
VR is the most immersive iteration of XR. It aims to replicate real-world scenarios. The user can interact with and navigate a lifelike, 360-degree virtual world. This typically involves a headset and haptic touch technology.
AR, or augmented reality, is less immersive but no less inventive. VR is like scuba diving – you go right beneath the waves and swim among the coral reefs. AR, by contrast, overlays some of those submarine features onto the world you see before you.
Think of a Snapchat filter. You're not taking a trip to a virtual dog pound – you're just popping on a pair of pooch ears.
And finally (for our purposes) there's MR, or mixed reality. This combines elements of both AR and VR.
In the world of design, VR could be a virtual tour of a prototype building. AR would give you the ability to handle, assemble, disassemble and annotate 3D objects as though they were there in the room with you. With AR, however, the room stays the same.
Bringing ideas to life with XR
The main reason that XR has the edge over 3D CAD and 3D printing is that a virtualised 3D asset can be modular.
Let's say you're designing a new kind of pepper grinder. A 3D printout or a 3D asset shown on a smart board can be labelled and rotated – but you can't take it apart and see where the peppercorns go.
But there's more. XR allows for rapid prototyping – and cheaper prototyping too. Products can be brought to market more quickly because the process of creating, modifying, discarding and improving prototypes has been turbocharged.
Virtual mock-ups like these can act as highly detailed, manipulable reference points during construction.
In short, XR narrows the gap between dreams and reality.
Present prototypes to stakeholders, clients and focus groups
Another huge advantage of XR is that it allows you to present your product to stakeholders, clients and focus groups with an unprecedented level of detail.
Designing a condo? You can treat your stakeholders to a 360-degree tour, walking them through a highly realistic simulation of a building that hasn't been built yet.
This can speed up the appraisal and approval process. You don't need to overpromise or underdeliver. You can show them exactly what you have in mind – and make any requested tweaks with impressive speed.
The same applies to focus groups. Letting the participants handle the object and take it apart leads to far more reliable feedback than passing around a 3D model – or looking at a revolving picture on a smart board.
Oh, and XR technologies are compatible with many devices. So whether you're using CAD, Unity or something else, you can integrate it with a virtual world.
Cut travel costs – and carbon
Finally, there's the whole issue of getting the team together when one person has to fly in from Bruges and another is taking the Orient Express.
It's not only expensive – it's also bad for the planet. And in our age of climate targets (from the Paris Agreement all the way down to your local library's recycling policy) this is more important than ever.
Equipping your team with XR headsets means that they can all be looking at the same 3D design no matter where in the world they are. They can all annotate it using in-call annotation. They can all split it into lifelike modules. And they can all handle the prototype as though it was there on the desk right in front of them.
In short, XR technologies can make the design process more flexible, tactile and lifelike than ever. In doing so, it can boost communication between you, your stakeholders, your clients and your focus groups – and it can help your company to be more sustainable, too.
SimplyVideo is an XR-enhanced
video call platform that's compatible with many devices. Interested in finding out more? Then why not
sign up for a free 30-day trial today?
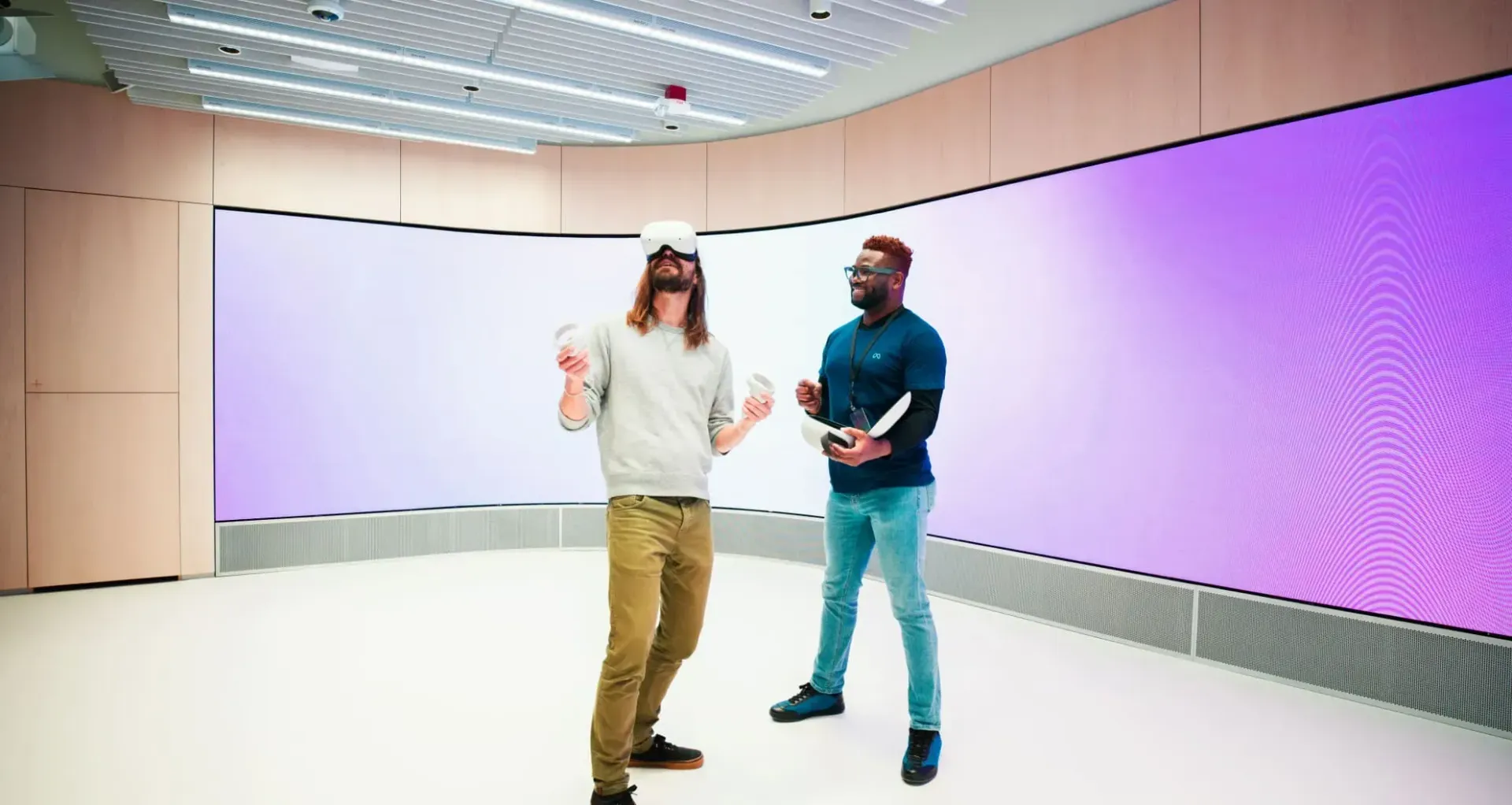